About Diversitech’s Technology
Since 1984, Diversitech has been a global leader in the Industrial Air Filtration & Dust Collection industry. Learn about our innovative technology.
About Diversitech
About Diversitech
Let Us Call You
For more information about any of our products or services,
please provide the information below and one of our experts will call you back shortly.
FRED Fume Tracker
The FRED Fume Tracker™ is the world’s first self-positioning Fume Extraction Arm for hassle-free
welding. It features patent pending technology that detects a weld arc and repositions the capture arm hood
above the fume source. Operators are able to eliminate time spent repositioning the hood and focus more on the
task at hand.
The Problem
Using traditional portable fume extractors, a worker must constantly reposition the hood above the fume source to ensure the smoke is captured. Since the extraction hood needs to be close the weld arc to be effective, the worker either pauses frequently to make adjustments or neglects to use the extraction arm altogether.The Solution
Using the FRED Fume Tracker every time the worker starts welding within the tracking window, the extractor hood automatically tracks to a precise position above the welding arc, ensuring fume capture at source. The welder can now complete the job without the hassle of constant arm-adjustments or the worry of inhaling hazardous welding fumes.How it works
Arc Sensors
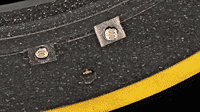
The FRED Fume Tracker capture hood is fitted with sensors that detect the welding arc and relay this information to the controller. Each time the unit is powered on, the controller performs a calibration that allows it to discern the difference between the ambient lighting conditions and the welding arc. The calibration only takes a few seconds, after which, the FUME TRACKER™ is ready to use.
Controller
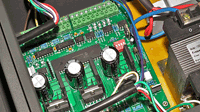
The controller accepts information from the light sensors, calculates the precise position of the welding arc using an innovative algorithm, and commands the servo motors to move the arm.
Servo Motors
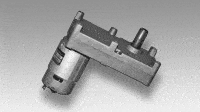
Three servo-driven motor articulations work in synchrony to robotically reposition the arm to a specific point, based on the calculations of the controller.
Field of Detection
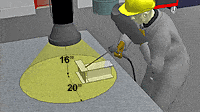
The FRED Fume Tracker has a sensibly wide field of detection. As long as the welder strikes a new arc within the sensing window, the arm will follow. If the task requires a weld outside the field of detection, the worker need only move the hood manually. The arm compromises several slip clutches to prevent the arm from being damaged when moved by the operator.
Injection Cleaning System (ICS)
Diversitech’s patented Injection Self-Cleaning System (ICS-360) reduces the total cost of
ownership of many of our dust collection products by:
Clean, dry, oil-free shop air, between 60 and 80 PSI, is
directed through a nozzle positioned inside the filter media. With a continuous flow of air parallel with the
filter, more than 80% of dust and debris is blown off.
- Extending filter life expectancy
- Improving aggregate filter efficiency
- Making routine service faster & easier
The Problem
All dust collector filters must eventually be cleaned and/or replaced. Depending on the filter media and the application, this routine maintenance can create a significant cost-center. Neglecting to service a dust collector filter increasingly strains the motor, and more importantly increasingly exposes workers to dust and fumes that are not being captured-at-source.The Solution
Diversitech’s ICS-360 technology injects compressed air from the inside of the cartridge through the filter, effectively blowing the dust and debris off the filter media. The solid pollutants then fall through slotted gates that closes at the end of the 8 minute cleaning cycle. Emptying the dust drawer periodically becomes a much easier and less costly maintenance exercise compared to manually cleaning the filter.How It Works
Continuous Air
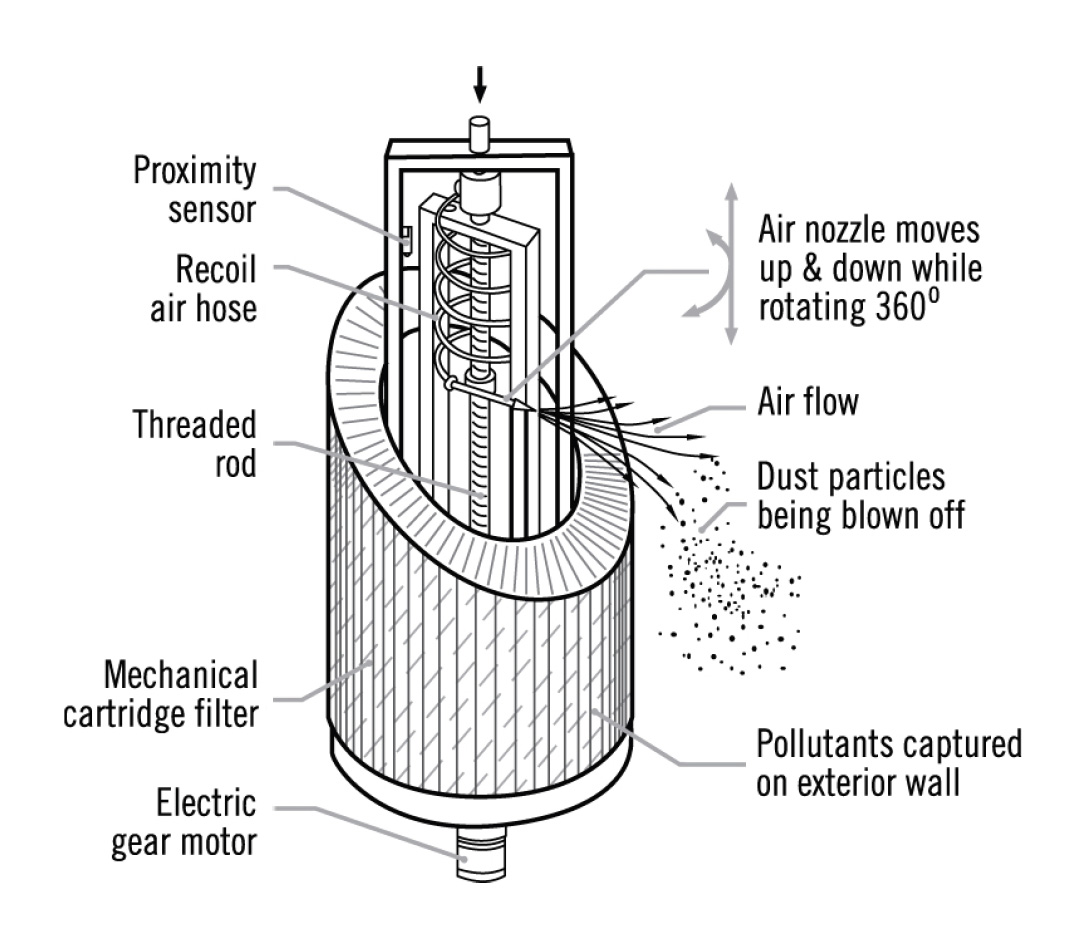
360° Rotation Top-to-Bottom
In order to blow continuous air over every part of the cartridge filter, the ICS-360 uses an encapsulated linear actuator and gear motor to move the nozzle 360° degrees top-to-bottom. No part of the cartridge filter escapes the thorough cleaning cycle.Dust Drawer
Slotted gates at the bottom of the cleaning chamber open to start the cleaning cycle. When the dust and debris falls, it settles into a dust drawer that can be easily serviced. At the end of the 8 minute cycle, the gates close to prevent dust re-entrainment onto the filter.Why The ICS-360 Works Better
Many other self-cleaning technologies rely on bursts or pulses of air from one end of the cartridge. The problem with any pulse system is the distribution of air across the filter media. A high cleaning efficiency is difficult to obtain with a pulse technology because invariably the bottom of the filter receives the bulk of the burst. Only the ICS-360 Injection Self-Cleaning System directs a continuous air stream at every inch of the filter media.Technology | Air Supply | Cleaning Efficiency |
---|---|---|
Cone Reverse Pulse | 60-80 PSI | 50-70% |
Reverse Pulse | 90-110 PSI | 10-30% |
Roto-Pulse | 120-140 PSI | 30% |
Venturi Reverse Pulse | 80-100 PSI | 30-50% |
Vibra Pulse | 80-120 PSI | 35% |
ICS-360 Injection Self-Cleaning System | 60-80 PSI | 80%+ |